Home
What's
Attorneys
Biographies
Businesses
Cemeteries
Churches/Worship
Civic/Social
Class Reunions
Classified Ads
Directories
Doctors/Dentists
Fire Department
Funeral Homes
Government
Histories
Holidays/Events
Libraries
Links
Maps
Medical
Neighborhoods
Newspapers
Obituaries
Parks
Pictures
Police
Post Office
Professional
Org
Radio/TV
Recreation
Schools
Sports
Tragedies
Transportation
Utilities
Veterans
|
FROM TIN BARS TO TOOTH-PASTE TUBES
The interesting story of A. H. Wirz, Inc., oldest U. S. manufacturers of
collapsible tubes, and one of our county's important
but little-known industries
What possible connection, even the most remote, you may wonder, could there be between a pile of tin "pigs" and an elaborate drugstore display of tooth paste? But the relationship is not as far-fetched as it seems on first thought. After all, the tubes and the blocks are basically of the same material, and therefore it's logical that tube containers could be made out of those solid blocks of refined tin. This process of metamorphosis goes on daily in one of Chester's flourishing industries, A. H. Wirz, Incorporated. Makers of collapsible tubes since 1870, Wirz is one of only 16 similar industries in America and the original pioneer in the field, being the first tube-making company in this country.
Collapsible tubes were invented back in 1841 in the United States through the brilliant imaginative foresight of one John Rand. However, the Germans were first to see its potentialities and began development and experimentation with it. When
A. Herman Wirz, manufacturer of surgical instruments, metal specialties and sprinkler tops, visited the Vienna Industrial Exposition in 1870, he saw the rich commercial value in the tube and took back to America plans for collapsible tube-making machinery. Its installation in the Philadelphia plant proved a successful business venture. By 1885, tube-making supplanted the former Wirz outputs. In 1914, growth of the plant necessitated the reorganization of the Company into a corporation and the removal of the entire plant to Chester, which has been the home center ever since. Wirz branch offices are located in four states-New York, Illinois, California and Tennessee - and in Havana, Cuba.
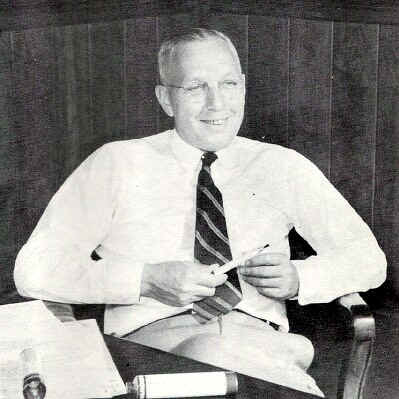
H. S. Darlington, President of A. H. Wirz, Inc.
Today, 200 employees are on the Wirz payroll; the tubes are shipped to every state and exported to many far-flung regions of the world; and numbered among the sales accounts receiving Wirz tubes are many well-known companies as, for example, Colgate-Palmolive Peet. A. H. Wirz presided over the Corporation until his death in 1929 when H. S. Darlington, (see photo above) succeeded him. Six years following his graduation from the University of Pennsylvania, Mr. Darlington entered the production department of Wirz and has been in the tube business ever since. Like his predecessor, Mr. Darlington carries on the pioneering spirit in tube-making.
In the factory's storeroom lie piled high, heavy bar "pigs" of tin, stamped either "Strait Settlements" or "Dutch East Indies." All of the tin is imported from the Far East. Even South America's Bolivia ships its tin ore to the Far East for refining. And from that distant point, the metal is exported to the United States. One can only speculate on the effect of the European conflict on the tin trade. It seems highly probable that with the concentration of the supply in the Orient, some agreement will be made between our government and. the Bolivian for the subsidization and refining of South American tin in the United States. Furthermore, aside from the mined metal. a second source of usable metal is reclaimed scrap tin. Electrically refined, the scrap becomes the purest and incidentally the most expensive form of tin on the market. With emphasis on the expense of reclamation, it is doubly interesting to wonder just what will happen in the tin export-import business
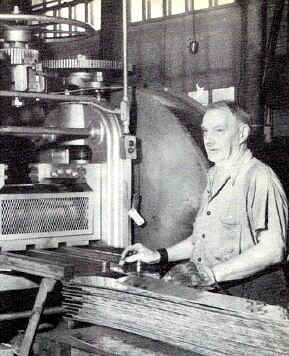
From the storeroom the bars of tin are brought into the foundry to undergo the first change of the dozen or so operations involved in transforming "pigs" into tubes. The tin is dumped into four huge pots, heated to a temperature of 750.F. Under such intense heat, the tin melts rapidly and
Robert Keever, (above left) scoops the molten liquid into a ladle and pours the hissing "soup" into a series of molds. When cool, the molds have formed plates - one inch thick, five inches wide and twenty inches long. Once around in the pots does not satisfy the demand for liquid tin and so R. Keever refills them on an average of fourteen to fifteen times per day, although all four pots are not in constant use.
Sam Rinehart (above right) who has been with the Company for 56 years, runs the molded plates through a roller until they are pressed out flat to a predetermined thickness. This thickness depends upon the actual length of the tubes to be made. For the average order it is one quarter inch.
Jack George (below) guides the strips through a machine that punches out metal slugs, each of which will later become a tube. The metal strips are now nothing more than scrap tin and are shunted back to the fiery foundry for remelting. About a quarter million slugs are holed out each day.
This machine punches out slugs to become tubes.
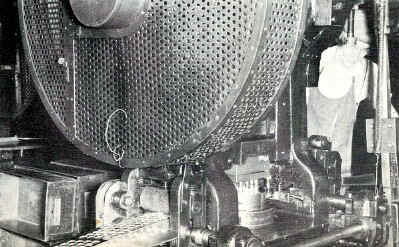
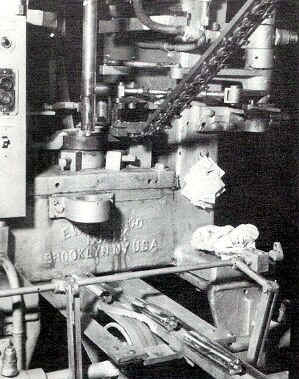
Numerous slugs whirl about in the tumbling machine's bucket-like depths (above left) until rough edges are smoothed and a film of lubrication oil glosses the tumbling slugs.
In order for the slugs to yield the tubes, they are placed in the feed hopper of an extrusion machine (above right). As the slugs are fed into the die, a swinging mandrel strikes them with a pressure varying up to 250 pounds, depending on what size tube is to be made. Instantaneously the tin receives the
impression of the die, and the tube's neck and shoulders are formed. The remaining metal is extended upwards to form the side walls of the tube. Thus the extended tin fits around the plunger and the tube assumes its familiar shape. A blast of compressed air blows the tube from the plunger onto a conveyor belt. Extrusion can be likened to the violent shoving of a stick into the mud. As the stick jabs downward, the mud
wells up and around its sides. At the rate of 50 tubes per minute, the extrusion process sets the pace for further tube detail production throughout the plant. In size the manufactured tubes range from the smallest, 3/8" x 1", to the largest, 2" x 10". On a reduced scale the making of the tin caps is similar to the tube-making. Bakelite tops which the Company does not itself manufacture, are extensively used, but the lining is glued into either type cap head at the Plant.
The conveyor belt carries the tubes to the trimmer's machine where the threads are cut around the neck of the tube and the ends are evened off. Traveling on a continuation of the same belt, the tubes pass to the paint operator who applies the tube's base coat or over-all color.
Mrs. Ann Gray (below) paints 60 tray-fulls daily.
Coating the tubes
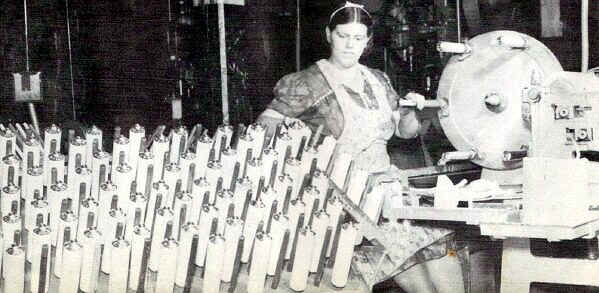
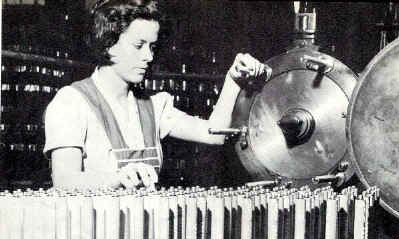
Printing designs on the
tubes
The tube could now be shipped away to be filled with the ingredient contents, but the Wirz treatment also includes printing the tube decorations by the offset process as demonstrated by
Beatrice McCallister (above). In printing the design she can use up to five different colors. As an aid in
working so closely with color combinations, the printing department is illuminated by overhead fluorescent lights. With the light rays falling directly on the scene of activity, an impression of daylight is created and colors are seen and judged in their true light. The decorated tubes are placed on trays which are stacked up in racks, filling a good part of the room. Girls remove the trays to long tables. There the tube caps are screwed on and the tubes packed upside down in cartons, as illustrated by
Mary Bradley (Below, left). When a carton is full of tubes, the effect is similar to that pictured at the lower right. This explains, to those who may have thought they were rolled flat and the end sealed, that the empty tubes retain their round shape and are left open at the bottom. In the factory which manufactures the trademarked contents, be it cream or liquid, the filler is poured into the tube's open end, and the aperture closed securely. And so what squeezes out of a tube from the top was put in from the other end!
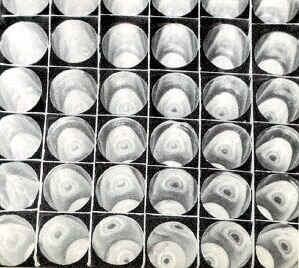
Screwing on the cap Carton of tubes
Every day's mail, going across the executive desks of A. H. Wirz, Inc., contains some inventor's ideas for the further perfection of, or a further use for, collapsible tubes. Only very rarely does such an idea ever prove to be of practical worth. The self-feeding, brush-tipped nail polish set shown (below left) is one brain wrinkle that proved an exception.
Victor Hall, in collaboration with A. H. Wirz, perfected this way of applying nail enamel, cuticle softener, polish remover, or nail creme to the nails. A squeeze of the tube and the contents ooze out on the applicator tip ready to anoint the finger nails. Nail polish brushtubes constitute only a small proportion of the many uses for collapsible tubes which are made in the Wirz plant. A model display of the heterogeneous collection of tubes shipped out from the plant is pictured (below right). "A tube for every purpose" could well be the company's motto. In general, all of the tubes are manufactured from anyone of three metals. Tin is used for the food, medical and cosmetic containers. Lead is used for such materials as artists' colors and rubber cement. Larger sized tubes, such as those for brushless shaving cream, are made of aluminum, and tin-coated lead is sometimes used instead of plain lead because it gives a better appearance. Of the Wirz tubes, about eighty per cent are tin
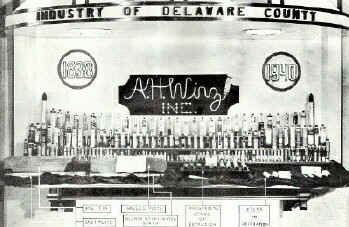
Self-feeding nail polish set A few of the many types of Wirz tubes
The next time you force that last bit of shaving cream to the brush; or massage the remaining bit of cream on your face; or smear the last drop of oil color on an artist's canvas; and then throw the mangled, empty tube away, remember the now useless hull perhaps had its very useful beginning at A. H. Wirz, Incorporated - one of Delaware County's important industries.
From From The Delaware County Advocate - October 1940
Thanks to Harvey S. Martin
Back to top of this page
|